REPOSAL® Winder Releases Coded Teach Winder Control System
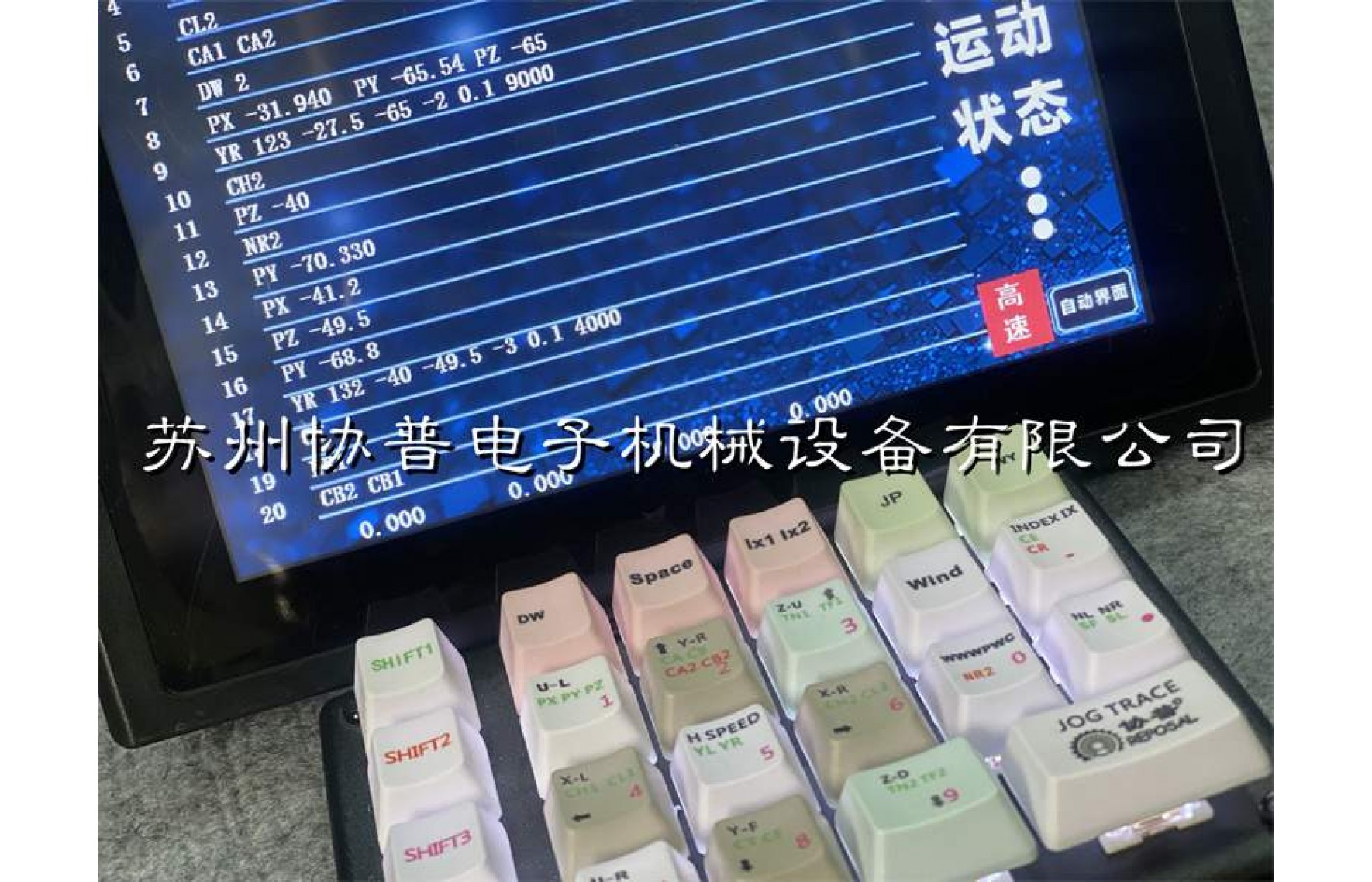
REPOSAL® Winding Machine Releases Code-Type
Teaching Winding Machine Control System
REPOSAL® Winding Machine, a domestic coil intelligent manufacturing solution provider, has launched its new generation of code programming teaching type winding machine control system that is more open, intelligent and highly autonomous for coil winding enterprises - REPOSAL® Winding machine SP500-R5 system. Compared with the traditional dialog-type winding machine control system, the SP500-R5 system has achieved major breakthroughs in operation logic, technical architecture, and function implementation. Features.
The SP500-R5 system adheres to the concept of "openness and intelligence". Based on the functions of the traditional dialog-based winding machine control system, it integrates the actual needs of the winding factory, and is committed to realizing the coil winding process programming process from the traditional parameter dialog. A major innovation and upgrade from control to code teaching programming.
REPOSAL® winding machine SP500-R5 system is an ingenious work combining the progress of the times and insight into the needs of users. It is based on the increasingly urgent needs of coil winding enterprises for flexible production.
Concise instruction set, special function keyboard, code programming, instant editing, hand-held teaching will greatly help coil winding enterprises to make the production process highly flexible, promote the automation, digitization and flexibility level of coil enterprises, and bring great benefits to customers. Important values such as "cost optimization, manpower reduction, safety and stability".
Meet industry challenges with continuous innovation
The real needs from coil companies are also the key force for change. For example, coil companies receive more and more orders, types and specifications, forcing companies to have higher and higher requirements on the flexibility, openness and maintainability of the winding machine control system;
Therefore, there is no doubt that the current coil winding enterprises urgently need a more advanced control system product to support the flexible production of coils in the future. Challenges made to key practices.
Mission and vision drive REPOSAL® winding machine code programming teaching type winding machine control system
The release of SP500-R5 system this time is undoubtedly another big step on the road of REPOSAL® winding machine product innovation. Quality development is of great value!
Related Post
REPOSAL® releases layer-wound high-voltage package full-automatic interlayer insulation winding machine
REPOSAL® releases layer-wound high-voltage package full-automatic interlayer insulation winding machine
Suzhou Xiepu Electronic Machinery Equipment Co., Ltd. successfully released the SP-D102M7 model of layer-wound high-voltage package automatic interlayer insulation winding machine-this model greatly improves the winding efficiency of layer-wound high-voltage package coils, and the coil is consistent Sex. The REPOSAL® winding machine reduces the winding cost of the layer-wound high-voltage package. In the new model, it has added a compact insulation belt automatic cutting mechanism, and high-quality solutions such as dynamic balance performance after multiple skeletons are wound.
REPOSAL ® winding machine Honeycomb coil winding machine
REPOSAL® numerical control honeycomb winding
machine, specially designed for honeycomb inductor coil, honeycomb coil with
its small size, small distribution capacitance, and large inductance in some
special occasions has irreplaceable. All of these excellent properties are due
to the unique structure of the honeycomb coil,
Traditional honeycomb winding machine is to
rely on a set of complex gear system to achieve the function, if you need to
wind different honeycomb coils, need to manufacture and replace different
gears, quite cumbersome and very low efficiency, REPOSAL® CNC honeycomb winding
machine uses high-precision control system, with specific algorithms, high
precision, fast speed, through different Settings can be wound different
widths, different fold points, Different number of turns of honeycomb coil, let
you wind honeycomb coil handy.
The inductance of the honeycomb coil is large,
mainly because of its special structure. After it is wound, from the
appearance, it is like a honeycomb, formed by the regular winding of coils to
form a honeycomb, in this one honeycomb, the magnetic flux of each honeycomb is
interconnected, and the magnetic flux density of these small magnets changes
with the change of time and position, just like the food in a honeycomb. This
distribution of magnetic flux pores makes the inductance of the honeycomb coil
larger, because it has more magnet interaction, thus forming more magnetic
flux, improving the permeability of the current, making the inductance
increase.
At the same time, since the magnetic flux of
each small magnet in the honeycomb coil is interconnected, the inductance can
be increased by increasing the size of the honeycomb. The larger inductance of
the honeycomb coil is due to its shape and the distribution of magnetic flux
pores, rather than due to the increase in resistance.
The insulated wire wrapped around the honeycomb
coil can be a single strand of enameled wire, or can be multiple strands of
enameled wire or silk-covered wire.
People are usually curious about how this kind
of coil is wound out, and the following is a demonstration of the CNC honeycomb
coil winding machine developed by our company.
REPOSAL®successfully releases hot micro flowmeter winding machine
REPOSAL®successfully releases hot micro flowmeter winding machine
----------solve the problem of heat pipe coil winding process
Flowmeter is one of the commonly used instruments in industrial production, the most common such as all kinds of water meters in life, gear water meters, electromagnetic water meters, ultrasonic water meters, etc., according to the different industry applications, chemical, petroleum, pharmaceutical, food and other industries are also widely used, can measure the volume or quality of various fluids through the pipeline in a given time. Easy to measure in each fluid automation control.
However, in medical, aerospace, military and other fields, we may need to measure tiny fluid flows, and in microfluidic processes, micro-thermal flow meters are also necessary, which can measure very small fluid flows, thereby helping researchers control the flow of fluid in microfluidic devices and optimize device performance.
Another example is the flow control of pure oxygen fluid in the ventilator, the flow control of the medical dosage ratio, the flow equivalent is very small, and at the same time, it requires extremely high measurement accuracy, so the thermal micro-flow meter should appear according to demand.
The thermal micro flowmeter is mainly made of the principle of capillary heat compensation. In the thermal micrometer, the fluid passes through a small pipe, and on the outer wall of the pipe, the thermal micrometer winding machine is used to wind a very small electric heating coil, which usually uses a fine platinum resistance wire, with a diameter between 0.02 and 0.05mm. When the fluid flows through the platinum resistance heating coil, the temperature of the fluid increases slightly. At this time, another set of platinum resistance coils wound by the thermal micro-flowmeter winding machine can sense a higher resistance, and the controller converts this resistance value into a flow value.
The diameter of the platinum resistance coil in the micrometer is very small, and the texture is fragile, and it will heat up after being energized. When the fluid passes through the capillary of the flowmeter, the flow will take away the heat of the platinum resistance coil wound by the hot micro-flowmeter winding machine, resulting in a decrease in the temperature of the platinum resistance coil. In order to keep the temperature of the platinum resistance coil stable, the micro flowmeter will provide a certain current according to the measurement needs to maintain the temperature of the hot wire at a constant operating temperature. By measuring the change in current provided to the hot wire, the mass flow rate of the fluid can be obtained.
Thermal micro flowmeter has many advantages, the main advantage is high accuracy, can measure the flow range of small small fluid, the accuracy can usually be within 1%. Moreover, it is small in size and can be easily designed into module units for convenient arrangement. It can also directly output electrical signals, and the communication with the data collector is convenient.
However, its manufacturing difficulty is high, especially the platinum resistance heating coil, the need for hot micro-flowmeter winding machine, in a very small diameter capillary wound diameter 0.02-0.05 platinum wire, the small diameter of the platinum wire itself is more fragile, the capillary also needs to overcome the radial displacement caused by the tension of the platinum wire during the winding process, and requires orderly arrangement. The tension is stable and the resistance is consistent, so the process is extremely difficult, and the current micro-precision winding technology of this hot micro flowmeter winding machine has been supported by sensor companies in Japan, the Netherlands and Germany for a long time.
The domestic precision winding mechanism manufacturing system from low-end to high-end, there are huge challenges, because there are shortcomings in the manufacturing equipment link, not only the problem of individual equipment such as hot micro flow meter winding machine, but the entire precision winding machine industry is lack of independent development conditions, the industry is keen to imitate foreign industry technology for a long time, and the user long-term superstition imported equipment, It is also one of the conditions for domestic winding machine enterprises to lack independent development, so the cost of domestic thermal micro-flow meters has been high.
REPOSAL® winding machine has successfully provided competitive solutions to the electron microscopy winding process
The main components of scanning electron microscope are electron optics system, signal collection and processing system, vacuum system, image processing display and recording system, power system and computer control system. The core part is the electron optical system, which is mainly composed of electron gun, electromagnetic condenser, diaphragm, scanning system, astigator, objective lens and various centering coils.
Reposal® winding machine As a professional supplier of precision winding solutions, we focus on the electromagnetic condenser, objective and astigmatic, because the main components are enamoured wire windings, and the precision and consistency of the windings are highly related to the image quality of the scanning electron microscope.
Electromagnetic lens coil.
The electromagnetic lens is mainly used to restrain the electron beam and it can be regarded as a convex lens in optics. Because the electron beam in a rotating symmetric magnetic field will be subjected to the Lorentz force, resulting in a focusing effect. Therefore, the quality of the enamelled wire winding coil that can generate this rotationally symmetric rather than uniform magnetic field and make the electron beam focus imaging is very important.
The enamelled wire winding coil in the magnetic lens, when the current passes through the coil, the pole shoe is magnetized, and a magnetic field is established in the heart cavity, producing a focusing effect on the electron beam. There are two kinds of enamelled wire winding in the magnetic lens, namely, the enamelled wire winding of the condenser and the enamelled wire winding of the objective lens. The lens near the electron gun is the enamelled wire winding of the condenser, while the one near the sample is the enamelled wire winding of the objective lens. General condenser is the high excitation lens enamelled wire winding, high excitation lens enamelled wire winding has many turns, a cylindrical multi-layer arrangement, requires good rotation symmetry
Study on the control of the speed curve of the coiling machine for precision coiling machine
Your factory is using a traditional winding machine, your wire machine structure is reasonable, high mechanical accuracy, the motor is also used a big brand of motor, but in the winding of precision coils, there will be a high defect rate, you carefully analyze before improving various factors - equipment structure, processing accuracy, tooling accuracy, skeleton accuracy, enamel wire quality, tension control, etc. But it still doesn't solve the problem. But to tell you that it's not just a hardware problem, but an algorithm problem, may surprise you. Because in your opinion, every time the spool is transferred, the spool has a corresponding response, but in fact, you may not have considered that in the winding process of the precision coil, the wire guide pin is connected at both ends of the coil, and the sudden change in speed may cause the coil to cross the line and be raised. These defects can degrade the performance of the coil.
To solve this problem, we propose an acceleration and deceleration method based on 5-segment S-curve. The algorithm uses linear acceleration or deceleration at the end and end of the line motion control to help reduce coil defects. We first verify the feasibility of the algorithm by using ADAMS software. The software simulates the motion of the precision winding coil and obtains the velocity curve and displacement curve during the motion. Later, the experimental results show that the method of adopting S-curve in the alignment speed control can reduce the coil defect by up to 50%. This shows that the 5-section S-curve motion control algorithm is a promising method to improve the precision and efficiency of the winding process of electric precision coils. By using this algorithm, coil manufacturers can reduce the risk of coil defects and improve coil performance.
Winding machine is a special production equipment for precision winding coils. They can be divided into stator winding machine, flying fork winding machine, ring winding machine and flat winding machine according to the working mode and object. Different types of equipment are suitable for the production of different objects. For example, the stator winding machine is mainly used to produce motor stator coils, while the parallel winding machine is used to produce electromagnetic switching coils.
Ordinary algorithm of parallel winding machine in the production of precision winding coil products, although our mechanical structure, parts processing accuracy has been done very well, but often there is a problem of low wiring accuracy. In the process of winding a line coil, there are two main movements, one is the rotating movement of the skeleton, which is called winding movement, and the other is the translation movement of the guide needle, which is called wiring movement, and wiring transport is matched with winding movement. After years of technical accumulation, we analyze that the leading role in the alignment accuracy is the alignment movement of the guide needle. Therefore, if you want to improve the alignment accuracy of the coil, you need to optimize the alignment movement of the guide pin.
In fact, we have always believed that the winding machine is equivalent to the lathe in the electrical industry, its importance is self-evident, so for its accuracy, there have been many experts and scholars to study this.
Some people studied the mathematical model of precise alignment based on axial pressure compensation around the axis in the process of alignment. The axial pressure was used to improve the alignment regularity of the coil, and the mathematical model was established according to the analysis of the end point of the coil alignment, which improved the alignment accuracy of the coil.
Some people use the 5-section S-curve control algorithm and the 7-section S-curve control algorithm respectively in the research. In motion control, the 7-section S-curve is more complicated than the 5-section S-curve control. This method has achieved more results in the field of CNC machining, but it is not mature in the field of winding machine.
The tension instability caused by the friction between the enamelled wire and the conductor nozzle during coil winding has been studied, which leads to the uneven wiring of the coil and the breakage of the enamelled wire.
Some people have studied the low efficiency of the winding machine in the traditional winding control because of the inertia error in the process of the winding machine. Instead, the servo motion wiring and the inertia error supplement are used to improve the control efficiency of the winding machine.
PLC control is commonly used in the winding machine wiring control system, through PLC control servo motor can realize the winding machine wiring control, both PLC control stability and high precision servo motor advantages. However, there is a sudden impact of guide pin speed in the coil alignment of parallel winding machine, so it is necessary to further optimize the change of guide pin running speed to improve product quality and the smoothness of wire alignment speed. The S-curve algorithm is a kind of smooth transition of speed in the process of motion, which is often used in machining to solve the problem of breaking the tool caused by speed impact and improve the precision of machining products. In the winding machine, the speed of the guide needle can be changed into an arc smooth transition by controlling the movement track of the guide needle, improving the alignment accuracy and product quality.
To sum up, an algorithm based on 5-segment S-curve motion control is proposed to solve the problem of velocity shock in the process of coil alignment by analyzing the law of coil alignment. ADAMS software is used to simulate the trajectory of the guide pin to verify the feasibility of the algorithm. And the application of the example proves that the 5-section S-shaped curve can effectively solve the phenomenon of crossing and protruding in the process of winding, and improve the precision of winding.
Coil wiring principle
The winding method is flat winding, that is, the enameled wire moves synchronously with the guide pin and always keeps perpendicular to the skeleton during winding. The frame is driven by the winding motor with the guide needle movement, the enameled wire is wound on the skeleton, in which the guide needle is located in the wiring arrangement mechanism and the winding mechanism are two independent mechanisms. The winding mechanism is divided into three stages according to the motion process of the guide pin, namely acceleration and deceleration stage, uniform speed stage and end point return stage. The acceleration and deceleration stage can be divided into two parts: acceleration stage and deceleration stage. In the early stage of the alignment movement, the guide pin speed from zero to uniform speed belongs to the acceleration stage. At the end of the alignment movement, the process of decelerating until the speed reaches zero is a deceleration stage. The middle constant velocity stage is the constant velocity motion stage of the guiding needle. The terminal reentry stage is a process in which the guide needle accelerates backward again after slowing down and stopping. Here we explain:
Acceleration and deceleration stage
In order to arrange the lines evenly, the two movements of guide pin movement and skeleton rotation should meet certain coordination relations during acceleration and deceleration stage. The time for the guide needle to move one diametral width distance must be equal to the time for the skeleton to rotate once, that is, the guide needle to move just one diametral distance when the skeleton rotates once.
REPOSAL® Winding machine Optimum design of CNC winding machine for large power transformer
In the manufacture of power transformers, winding the transformer coil is a super important step, you think, the transformer coil is wound more firmly and neatly, the strength of the transformer and the ability to protect against short circuits can be greatly improved. However, most of the current transformer winding machines have to rely on manual extra sorting of the coil, the entire equipment is low in automation, and the production efficiency is not high, so the development of an excellent large transformer winding machine is a crucial thing for our company.
We have studied the main shaft technology of transformer winding machine, the relationship between compaction force and winding quality, and the control of compaction force. According to the principle and process flow of transformer winding, we put forward a whole design scheme of large transformer winding machine, including mechanical structure and electrical control. Mechanically, we simplify the complex structure of traditional transformer winders. In terms of electrical control, we ensure the stability of the motor when it starts and stops, and ensure that the winding coil is evenly tightened during the winding process. For the core parts of the transformer winding machine, spindle system and pressing device, we have calculated and selected the types and parameters. With the compaction device, we are able to provide real-time axial and radial compaction forces during the winding process of the transformer winding, which is very effective for improving the tightness of the winding.
The static analysis of the radial compaction device of the winding machine is also carried out by using finite element method, and the structure optimization is carried out according to the analysis results. We find that as the number of layers and turns of the winding increases, the required axial and radial compression forces change accordingly. By analyzing the experimental data, we find that there is a maximum value and a minimum value in the range of quality requirements, and it is the most reasonable choice to make the compression force approximately proportional to the number of layers and the number of turns.
The large transformer winding machine developed by our company has been preliminatively debugged and put into the market. After testing, the performance parameters of this transformer winding machine are in line with the design requirements, and the operation is stable and efficient. It can be wound to make a tight and regular transformer winding coil, and has been fully recognized by the market.
As a power grid equipment, power transformer converts voltage through the electromagnetic induction between the winding coils of the transformer. With the continuous development of the market, higher requirements are put forward for the manufacturing level of transformers, and the market needs more energy-saving and efficient transformers. Therefore, the optimization of the transformer manufacturing process is particularly critical. Quality and performance depend on the process equipment. The technical level of the transformer winding machine directly reflects the manufacturing level of the transformer. Therefore, accelerating the development of transformer winding machine is an important guarantee to improve the performance of transformer.
The winding coil of the transformer is the core component of the transformer and constitutes the electromagnetic induction part of the transformer. It generally includes high voltage winding and low voltage winding, respectively connected to the high voltage grid and low voltage grid. The winding of large power transformers usually adopts concentric winding, that is, the high and low voltage transformer winding coils are centrally set on the core column. The manufacture of transformer winding is the core process of transformer, and its quality plays a crucial role in the performance of transformer, affecting the appearance of transformer size, weight, mechanical properties, insulation and heat resistance and other important indicators.
In the past, the production of transformer winding coils relied on manual, and workers had to wind insulated wires manually to the winding die frame in accordance with the process requirements. Turns calculation also have to rely on manual, this old-fashioned method is inefficient, and because the worker's skills are not strong enough, the quality of the winding coil is poor, the number of turns may be miscalculated or missed, and ultimately lead to the finished winding coil performance can not be guaranteed. Later appeared semi-automatic transformer winding machine, which is driven by the motor to rotate the spindle to wind the transformer winding coil, although it improves the production efficiency, but the wiring work still has to rely on manual, only suitable for flat winding transformer winding coil winding, and winding head winding, welding and other operations must still be completed manually, so the product quality is not stable.
Later, with the emergence of TTL logic gate circuits, in the mid-1970s, with the development of CMOS technology, various types of equipment program control a large number of applications of digital integrated circuits, Western countries and Japan and other industrial powers have emerged CNC winding mechanism manufacturing industry. These CNC transformer winding machines represent the advanced level of winding mechanism manufacturing technology, especially the winding equipment produced in Japan, Italy, the United States and Germany is the leading technology.
Now the transformer winding machine as the core parts of the transformer production equipment, the market demand is very large, and the transformer manufacturing enterprises at home and abroad attach great importance to the development and application of advanced technology of transformer winding machine. Domestic transformer winding machine production enterprises are small, insufficient technical reserves, limited research and development funds, so there is still a big gap compared with foreign advanced products, the market share is low, unable to compete with foreign countries. To solve the key technical problems of transformer winding machine is the key to improve the quality of domestic winding equipment and enhance the market competitiveness. In order to meet the demand of transformer manufacturers for high quality and low price winding equipment, especially large transformer winding machine, on the basis of learning from foreign advanced experience, combined with domestic research results, the development of large transformer winding machine has important significance and practical value.
REPOSAL® winding Machine successfully overcomes the polarization grid precision winding technology
Since these polarized wire grids, which are wound by precision winding machines, have no underlying substrate, they have the advantage that they are not affected by substrate related dispersion and absorption, and there is no beam deviation during transmission. This provides a thin, compact and versatile polarization element with a high degree of polarization over a wide transmission range.
At present, because there is no professional winding machine, most of the polarization grid used in our country is imported polarization grid, and the price is expensive; However, the domestic processing method of wire grid mainly uses manual winding, which has low precision and long production cycle. At the same time, the winding machine at home and abroad is mainly used in electronic components, sensors, etc., the control variable is relatively single, and the main control mode is tight layout, even the high precision winding machine, there are few equal spacing layout for the polarization line grid, so the accuracy can not meet its needs. Therefore, it is very important for the coiler to overcome the polarization grid precision winding technology.
REPOSAL® has successfully released a radiofrequency ablation catheter winding machine
Radiofrequency ablation has ablation and cutting functions, and the main therapeutic mechanism is thermal effect. Radio frequency refers to radio frequency, frequency up to 150,000 times per second of high frequency vibration, but it does not belong to the division of bands in radio communication.
The coiling process is completed by continuous test and optimization of the coiling machine.
The working flow of this winding machine is as follows:
1. The active wire feeding device of the radiofrequency ablation catheter winding machine ensures that the wires are constantly connected and not tied.
2. Double fold section A measurement line.
3. Manual folding head.
4. Manually fix the thread head (Two schemes are tentatively proposed for fixing the thread head)
4.1 Fix the starting position with glue. The fixture locks the PEEK tube.
4.2 Kangtong wire is hung on the feature of steel pipe. Glue to fix the ends after wrapping.)
5. Press the start button of the radiofrequency ablation catheter winding machine to wrap.
6.(During the winding process of the radiofrequency ablation catheter winding machine, both AB and AB segments have adjustable tension)
7. Wrap the jump grid to the specified position (the specific hop length can be set, and the rotation Angle can be set.
8. After the radiofrequency ablation catheter winding machine is finished, the feeder stops at the end and maintains tension.
9. Fix the end of the line by manual dispensing
10. Both ends of the radiofrequency ablation catheter winding machine are coaxial, and the rotation direction is synchronized.
11. Adjustable pre-drawing force is required at both ends of the locking shaft core.
REPOSAL® winding machine wire guided missile fiber winding forming technology has made a new breakthrough
REPOSAL ® winding machine wire guided missile fiber winding forming technology has made a new breakthrough
Fiber optic guidance of wire-guided missile is a closed-loop guidance and control of controlled missile by bidirectional transmission of information and control signals between missile and launcher using special fiber optics.
Fiber optic guidance belongs to the wire guidance of remote control guidance, its advantages are not only high precision, strong anti-interference ability, can be equipped with optical cable shaft, micro camera, missile launch tail will release fiber, can control the missile and obtain target information.
The winding and release technology of optical fiber is a key technology of optical fiber guidance. At present, we have not realized automatic production in the production of optical fiber winding in our country, so we rely on the winding technical personnel's proficiency very high. The cross-turns working procedure of the winding process is still mainly manual operation, low production efficiency, high error probability and low consistency.
In addition to other ways to solve the high speed release of optical fiber, an important way is to ensure the smooth release of optical fiber through optical fiber winding. Optical fiber winding technology is the requirement of the pointer to the optical fiber guided missile and the technology of winding the optical fiber on the spool. In view of the unique properties of optical fiber and the special use of optical fiber guided missile, optical fiber winding becomes a complicated technical problem. In the process of automatic winding, the technical difficulties related to the properties of optical fiber are as follows:
REPOSAL ® winding machine has successfully realized the coil preparation process of the frameless capillary magnetic liquid acceleration sensor
In particular, the non-magnetic material in the magnetic liquid will be subjected to a magnetic field force in the non-uniform magnetic field, which makes many magnetic liquid acceleration sensors can be designed based on this characteristic.
These characteristics make the magnetic liquid acceleration sensor has many advantages compared with the traditional acceleration sensor, such as no wear, high sensitivity and simple structure.
However, most of the existing magnetic liquid acceleration sensors use solid mass blocks as non-magnetic substances, and use coils to detect changes in inductance under different accelerations to obtain output signals. However, its disadvantage is that it leads to complex magnetic circuit and poor sensor stability.
A new solution emerged -- the capillary magnetic liquid acceleration sensor, good stability, simple magnetic circuit, accurate and reliable measurement results and long service life.
REPOSAL's successfully developed precision flexible Roche coil winding machine
Precision Flexible Roche Coil Winding Machine is a special equipment for winding precision flexible Roche coils. With the actual project as the background, Xiepu successfully developed a precision flexible Rogowski coil winding machine by decomposing the flexible Rogowski coil winding process.
The precision flexible Roche coil winding machine does not belong to the ranks of general numerical control equipment, but a special non-standard equipment. For this type of equipment, it is mainly reflected in a special purpose. Since the special purpose means that the market demand is not large, it is indispensable. For equipment manufacturers, the development of such special equipment is not favored, and cost control is very difficult.
In addition, the current domestic manufacturers of flexible Roche coils have limited demand for equipment. At the same time, if you want to control the pitch accuracy and alignment, the equipment research and development costs are relatively high, and the market risk is large. At the same time, for equipment users, their corresponding The supporting equipment and instruments are a large investment.
REPOSAL successfully developed string winding machine
REPOSAL takes the string winding machine as the research object and adopts the modal analysis method. Firstly, the vibration principle and the movement principle of the winding mechanism of the small string winding machine are discussed in theory. Based on the principle analysis, the vibration analysis of the ADAMS model of the small copper wire winding mechanism to study the vibration damping characteristics between the roller shaft and the frame is carried out respectively, and the wire winding mechanism of the string winding machine is made using ANSYS software. Modal analysis was carried out for normal operation. Through analysis, the vibration characteristics of the winding mechanism of the string winding machine under normal working conditions are obtained respectively to optimize the vibration damping measures of the winding mechanism. At the same time, the mechanical characteristics of the thin wire and CNC under the normal working state of the CNC winding mechanism are analyzed. , Optimizing the feasibility of applying the CNC cable winding mechanism to the string winding machine cable winding mechanism.
Congratulations on our winding machine successfully passed the EU CE certification, enter the international market
Congratulations on our winding machine successfully passed the EU CE certification, enter the international market
In response to the international market's requirements for the safety and quality of our winding equipment, recently, our series of winding machines have won the CE certification issued by the European Union certification body. This marks the recognition of the EU market for the |REPOSAL® winding machine, which means that our company has the ability to provide more professional and high-quality winding machine equipment for the international coil market, and further enhance the company's international competitiveness.
REPOSAL® Winding machine CE certification certificate
On the one hand, in response to the national "Belt and Road" call, REPOSAL® winding machine actively explore overseas markets. The passing of the EU CE certification not only opens the European market, but also the first step to open the global market, which means that the company's winding machine can be exported to various countries in the European Union, and the pursuit of free circulation of our winding equipment in the global scope has a positive effect on the company's expansion of overseas winding machine market and international business expansion. At the same time, it also provides safety and quality assurance for the sales of the winding machine in the domestic market, and enhances the brand influence of the winding machine.
Winding machine selection
In the narrow sense, the winding machine mainly refers to the winding machine of various enamelled wire coils, these coils may be transformers, relays, inductors, current transformers, various sensors, these coils can be seen everywhere in our lives, the common feature is to use enamelled wire winding, the difference is according to the design requirements, and the cost and efficiency requirements of industrial products, Its winding process is not corresponding, so derived from a variety of different winding machine, we show on the official website is only a part of the conventional winding machine, and some are customized, or special industries are not displayed, if you need to know, you can contact us.
Coils can be seen everywhere in our lives, such as the electric meter in the home, there are metering induction coils, trip coils in the circuit breaker, transformer coils in the community, various motor coils in industrial automation, various sensor coils, starting coils on the car, ignition coils, power motor coils on the bullet train, etc., it is no exaggeration to say that we live in a world of coils. There are so many coils, and the corresponding winding machines are different, so the winding machine is as important to the electrical world as the lathe is to the mechanical world.
There are so many types of winding machines, if you are not familiar with them, those selections have become a big problem, we now make a simple introduction from several aspects.
One is the winding method, which is generally divided into parallel winding machine, ring winding machine, and flying fork winding machine.