Design and verification of winding machine for precision voltage transformer
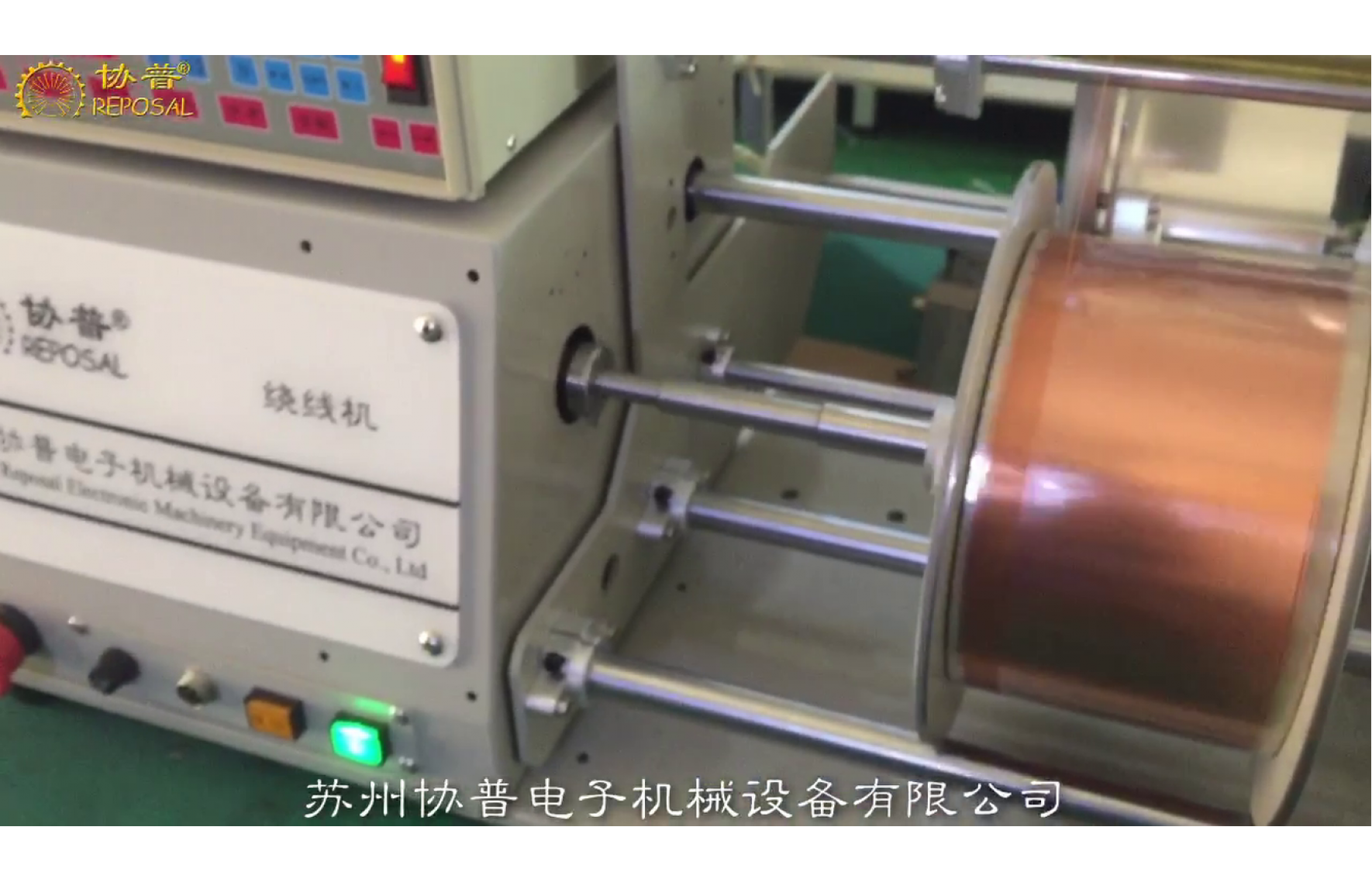
In power transmission and power supply systems such as power plants and substations, voltage transformers are an indispensable electrical appliance. The voltage transformer for measurement specifies the accuracy level of the voltage transformer according to the error generated when the voltage is changed. Voltage transformers of level 0. 2 and above are generally called precision voltage transformers, which are mainly used in the laboratory to expand the measurement limit with the standard meter for precise measurement of voltage, power and electrical energy; or as a standard to check low standards, Low-accuracy voltage transformer; it can also be used with standard meters to test the corresponding meters.
With the rapid development of science and technology and electronic application technology, the requirements for technical indicators such as the rated primary voltage and accuracy of voltage transformers are getting higher and higher, and the demand for various types of voltage transformers is increasing. In the past, voltage transformers were mostly manually wound with annular iron cores and thick enameled wires. The products were large and heavy. In the daily winding, processing and production process, the degree of mechanization was not high, the labor intensity of workers was high, and the production efficiency was low. It is necessary to improve the voltage transformer design process and develop a new type of mechanical equipment for winding the voltage transformer.
The structure of precision voltage transformer:
The precision voltage transformer is mainly composed of primary winding, secondary winding, iron core and insulating material. The primary winding is directly wound on the R-shaped ladder core, and the number of turns of the secondary winding varies with the change of the secondary voltage and the error level of the voltage transformer, ranging from tens of thousands of turns to hundreds of thousands of turns.
Design ideas of precision voltage transformer winding machine:
The secondary winding coil of precision voltage transformer has many turns, and the enameled wire used for winding is very thin, which cannot be completed manually. If mechanical equipment is used for winding, only the bobbin carrying the secondary winding can rotate, so that the enameled wire on the winding tool is wound on the bobbin fixed on the secondary winding in an orderly manner.
Since the power that the machine needs to transmit is low and the transmission efficiency requirements are not too high, the first-level transmission adopts belt transmission, and the flat belt transmits the movement and power of the motor to the main drive shaft.
Text box: 7 Youqian friction transmission has simple structure, stable transmission, convenient transmission ratio adjustment, and slippage when overloaded to avoid damage to the device. Therefore, the secondary transmission adopts friction wheel transmission, that is, the transmission wheel fixed on the main drive shaft and the secondary winding bobbin rotating friction, and the movement and power are transmitted to the secondary winding bobbin.
The main components of the winding machine
transmission
The power source of the voltage transformer winding machine is a DC brushless motor with a power of 0.6Kw and a speed of 6000 r/min.
The secondary winding coil is wound with high-strength poly enameled round enameled wire, the diameter of the enameled wire is 0.08 mm-0.1 mm, and the strength limit is about 882 MPa. If the revolving speed of the secondary winding bobbin is too slow or too fast, it is easy to break the enameled wire. Through empirical analogy, related tests, working characteristics of the transmission and specific working conditions, as well as the counting speed of the counter and other comprehensive technical indicators, select the small pulley diameter d1 = 32 mm, the large pulley diameter d2 = 80 mm, and the main drive wheel diameter d3 =40 mm, the diameter d4 of the secondary winding bobbin of various voltage transformers is approximately 120 mm.
transmission shaft
This machine is low-power transmission, and the shaft speed is not high. The drive shaft is made of 45 steel, quenched and tempered, the hardness is 217 HBS ~ 235 HBS, and the strength limit is 650 MPa.
The axial force of this bearing is not large, so the bearing adopts 6201 deep groove ball bearing. The circumferential direction of the bearing adopts .H7/k6 interference fit, and the bearing cover is used for axial fixation. The main drive wheel on the drive shaft and the drive shaft adopt a H9/h9 clearance fit, and are fixed in the axial and circumferential directions with M5 set screws.
The high-strength polycool enameled round enameled wire on the winding tooling needs to be continuously wound on the secondary winding bobbin. When the number of coil turns reaches the design requirement, the bobbin carrying the secondary winding must stop rotating.
This machine uses REPOSAL® precision winding controller to count the number of coil turns. The resolution of the number of turns is 0.1 turns. When the number of turns of the coil reaches the set number, the relay contacts will change position, stop counting or continue counting, so as to achieve the purpose of accurately counting the number of coil turns.
Improvement direction:
With the continuous improvement of the technical performance and accuracy requirements of precision voltage transformers, the number of turns of the primary winding and the secondary winding will increase, and the quality of the winding must also be improved, so as to ensure the inter-turn and layer of the primary winding and the secondary winding. The quality of the insulating material between the windings and the windings. Therefore, under the premise of ensuring that the enameled wire is not damaged, the rotation speed of the wire frame can be appropriately increased, and the wiring mechanism can be improved; or the copper clad steel wire can be used in the design of the secondary winding to improve its strength, bending resistance, toughness and Torsion resistance and vibration resistance.
in conclusion:
When the voltage transformer winding machine is used to wind the secondary winding of the 35 kV precision voltage transformer, a 0.8 mm high-strength poly-enameled round enameled wire is used, the number of turns of the secondary winding is 110,000, and the winding time is 300 min. , The transmission efficiency is 91. 5%, which meets the expected design requirements. During the winding process of the machine, all parts of the machine are in good working condition, the counting is accurate, and the number of broken enameled wires is very few. With the action of the guide wheels, the enameled wires can basically be arranged in each grid of the wire frame in an orderly manner.